Machining a titanium part is a process that can be intricate and time-consuming due to titanium’s unique properties, which include high strength, low density, and exceptional resistance to corrosion and heat. The exact time required to machine a titanium component depends on multiple factors such as the complexity of the part, the type of machinery used, cutting speeds, tooling material, and the specific alloy of titanium being processed. Generally, titanium machining requires longer processing times compared to other metals because of its hardness, low thermal conductivity, and tendency to cause rapid tool wear. These factors make titanium more challenging to work with, often necessitating slower cutting speeds and more frequent tool changes. However, advances in machining technologies, such as the use of high-performance cutting tools, optimized coolant systems, and specialized CNC equipment, have made it possible to machine titanium components more efficiently while still ensuring tight tolerances and high-quality finishes. As a result, titanium is increasingly used in aerospace, medical, and high-performance industries.
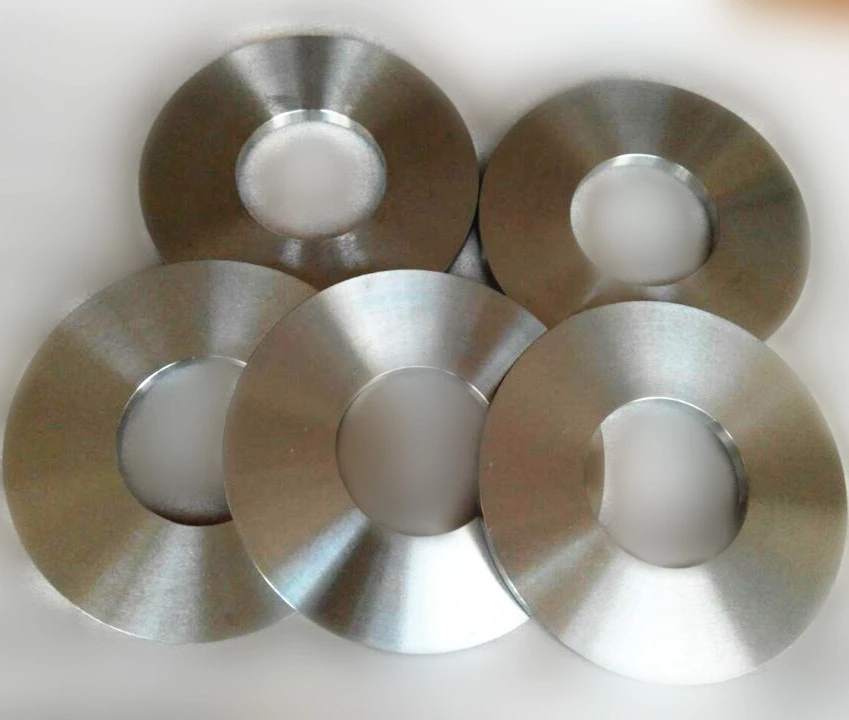
Why Titanium Machining Takes Longer?
Titanium is prized for its exceptional strength-to-weight ratio, corrosion resistance, and durability, making it ideal for demanding applications across industries like aerospace, medical, and automotive. However, these qualities also make titanium difficult to machine. The following factors contribute to the machining time for titanium parts:
- Heat Resistance: Titanium retains heat, making it essential to apply slower, consistent cutting speeds to avoid tool damage and maintain precision.
- Tool Wear: Titanium’s hardness accelerates tool wear, which may require frequent tool changes, affecting overall machining time.
- Work Hardening: As machining progresses, titanium tends to harden, requiring careful adjustments to maintain consistency and prevent workpiece damage.
Key Factors Affecting the Time to Machine Titanium Parts
Machining Process and Equipment
- Precision CNC Machines: Advanced CNC machines are often used to machine titanium accurately, allowing for optimal tool paths and feed rates that increase efficiency.
- Cutting Techniques: Multi-axis machines and high-speed machining techniques can reduce cycle times by allowing complex cuts and reducing repositioning.
- Cooling and Lubrication Systems: Effective cooling systems help to dissipate heat, preventing tool wear and material deformation, thus reducing delays.
Part Complexity and Size
- Geometry: Complex part geometries with intricate features require more machining time due to the precision needed.
- Thickness and Diameter: Larger titanium parts generally require longer machining times, as thicker sections necessitate slower speeds and more passes.
- Tolerance Requirements: Tight tolerances or fine surface finishes add to machining time as they require finer adjustments and slower speeds.
Tool Material and Quality
- Carbide vs. Ceramic Tools: Carbide and ceramic tools are commonly used in titanium machining because they withstand high temperatures and resist wear.
- Tool Geometry: Proper tool geometry helps in reducing friction, improving the efficiency of the machining process.
- Tool Coatings: Specialized coatings on cutting tools, such as diamond-like coatings, help reduce wear, allowing longer machining times before needing replacements.
Titanium Machined Parts: The Impact of Machining Strategies
Optimizing Cutting Speeds and Feeds
- Ideal Cutting Speed: Cutting speeds in titanium machining need to balance efficiency and quality to avoid excessive heat build-up.
- Feed Rate Adjustment: Fine-tuning the feed rate prevents work hardening and enables smooth cuts, which is essential for long, uninterrupted runs.
- Variable Machining Parameters: Adaptive machining strategies that adjust speeds and feeds can help minimize tool wear and ensure precision, reducing overall time.
Reducing Downtime with Efficient Tool Changes
- Tool Life Management: Monitoring tool wear proactively prevents unexpected delays.
- Automated Tool Changers: Multi-tool machines with automated changers reduce manual intervention, which can significantly save time.
- Tool Conditioning and Pre-setting: Ensuring tools are conditioned and preset can eliminate unnecessary downtime.
Advanced Cooling Techniques
- Flood and Mist Cooling: These methods help reduce heat buildup, ensuring faster and safer machining.
- Cryogenic Cooling: Using liquid nitrogen for cooling enhances the machining speed by maintaining low temperatures at the cutting zone.
- High-Pressure Coolant Delivery: Directing coolant under high pressure to the cutting zone effectively dissipates heat, allowing faster speeds without risking the quality of the titanium part.
Titanium Machined Parts: Best Practices for Faster Machining
Choosing the Right Cutting Tools
- High-Performance Inserts: Inserts with specific geometries for titanium enhance efficiency and lifespan.
- Coated Carbide Tools: These are particularly suitable for titanium as they withstand high temperatures and abrasive wear.
- Diamond and PCD Tools: In specialized applications, these tools improve accuracy and reduce machining times for titanium parts.
Optimizing Machining Paths and Techniques
- Trochoidal Milling: This technique enables continuous cutting with low radial engagement, ideal for titanium machining.
- High-Efficiency Milling (HEM): HEM reduces machining time by maximizing metal removal rates while preserving tool life.
- Adaptive Machining Strategies: Software-enabled strategies allow for real-time adjustments to optimize cutting paths, particularly useful for complex parts.
Minimizing Rework and Quality Control Delays
- In-Process Monitoring: Using sensors to monitor cutting conditions helps detect issues early and reduce rework.
- Quality Inspection During Machining: In-machine measurement tools can check dimensions in real-time, helping to maintain tolerances and minimize post-machining corrections.
- Reducing Setup Times: Using fixtures and automation for setups ensures accurate positioning, reducing the need for manual adjustments and inspections.
Conclusion
The time required to machine a titanium part can vary significantly depending on the part's complexity, the machining techniques employed, and the equipment used. Titanium’s unique properties, such as its high strength, heat resistance, and hardness, often make it more challenging to machine compared to other metals. However, by implementing optimized cutting strategies, selecting the right tooling, and using advanced cooling methods, it’s possible to achieve efficient and high-quality results. These approaches help minimize tool wear and heat buildup, leading to reduced cycle times and more consistent surface finishes. For businesses, adopting these techniques can lead to reduced downtime and improved overall productivity, which are crucial when working with demanding materials like titanium. If you'd like to learn more about our titanium machining capabilities or discuss specific requirements, feel free to contact us at rmd1994@yeah.net.
References
1. ASM International. Titanium Machining and Cutting Handbook.
2. Metalworking Industry Standards Council. Standards for Titanium Machining Processes.
3. Sandvik Coromant. Cutting Techniques for High-Strength Materials.
4. American Society of Mechanical Engineers (ASME). Principles of Metal Cutting and Tooling for Titanium.
5. The Machining and Cutting Institute. Machining Titanium Alloys: Challenges and Best Practices.
6. Metalworking World Magazine. Optimizing Machining Times for Advanced Materials.