Raw Material Preparation and Processing
Tungsten Ore Extraction and Beneficiation
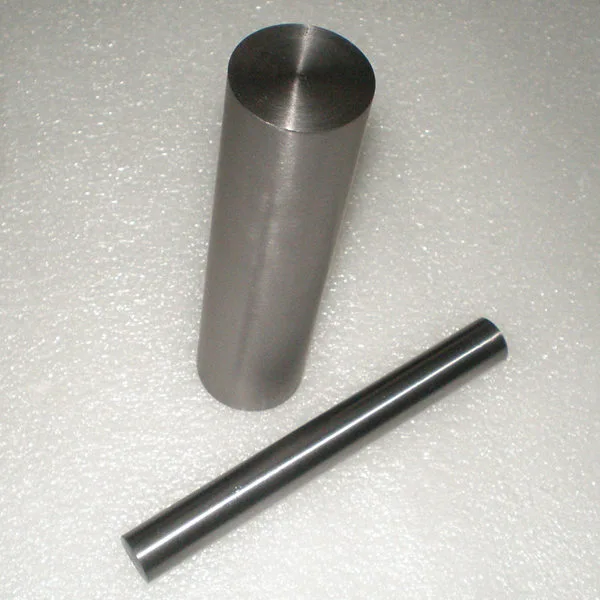
The journey of a tungsten bar begins deep within the Earth's crust. Tungsten ore, primarily found in the form of wolframite ((Fe,Mn)WO4) or scheelite (CaWO4), is extracted through various mining techniques. Open-pit mining and underground mining are common methods, depending on the deposit's location and characteristics. Once extracted, the ore undergoes beneficiation processes to increase its tungsten content. These processes may include gravity separation, magnetic separation, and flotation, which help remove impurities and concentrate the tungsten minerals.
Chemical Processing and Oxide Production
The concentrated tungsten ore then undergoes a series of chemical treatments to produce tungsten oxide (WO3). This typically involves digestion in sodium hydroxide or sodium carbonate solutions, followed by filtration and purification steps. The resulting sodium tungstate solution is further processed to precipitate ammonium paratungstate (APT), which is then calcined to form tungsten oxide. This intermediate product is crucial in the tungsten bar manufacturing process, as it serves as the precursor for pure tungsten metal production.
Tungsten Powder Production
The final step in raw material preparation involves reducing tungsten oxide to tungsten powder. This is typically achieved through hydrogen reduction, where tungsten oxide is heated in a hydrogen atmosphere at temperatures ranging from 700°C to 1000°C. The process results in fine tungsten powder with controlled particle size and morphology. The characteristics of this powder, such as particle size distribution and purity, play a significant role in determining the properties of the final tungsten bar product.
Tungsten Bar Manufacturing Techniques
Powder Metallurgy and Compaction
One of the primary methods for producing tungsten bars is powder metallurgy. This technique begins with the careful blending of tungsten powder with small amounts of alloying elements or binders, if required. The powder mixture is then compacted into a "green" bar shape using high-pressure presses. This compaction process helps achieve the initial shape and density of the bar. The green compacts are relatively fragile at this stage and require further processing to attain their final properties.
Sintering and Densification
Following compaction, the green tungsten bars undergo sintering, a critical step in the manufacturing process. Sintering involves heating the compacted bars to temperatures close to, but below, tungsten's melting point (typically around 2000-2500°C) in a controlled atmosphere. This high-temperature treatment causes the tungsten particles to bond together, reducing porosity and increasing density. The sintering process is carefully controlled to achieve the desired microstructure and properties of the tungsten bar. Factors such as temperature, time, and atmosphere composition are optimized to ensure uniform densification and grain growth.
Hot Isostatic Pressing (HIP)
For applications requiring exceptionally high-density tungsten bars, manufacturers often employ Hot Isostatic Pressing (HIP) as an additional or alternative processing step. In HIP, the sintered or pre-sintered tungsten bars are subjected to high temperature and isostatic gas pressure simultaneously. This process further reduces porosity and enhances the mechanical properties of the tungsten bar. HIP can achieve near-theoretical density in tungsten bars, making it particularly valuable for applications in aerospace and nuclear industries where material integrity is paramount.
Post-Processing and Quality Control
Machining and Shaping
After the primary manufacturing processes, tungsten bars often require additional machining and shaping to meet specific dimensional requirements. Due to tungsten's hardness and brittleness, specialized tooling and techniques are necessary for these operations. Computer Numerical Control (CNC) machining, grinding, and Electric Discharge Machining (EDM) are commonly used to achieve precise dimensions and surface finishes. The choice of machining method depends on the final application of the tungsten bar and the desired tolerances.
Heat Treatment and Surface Finishing
Heat treatment processes may be applied to tungsten bars to optimize their mechanical properties or relieve internal stresses. These treatments can include stress relieving, recrystallization annealing, or controlled cooling regimes. Surface finishing techniques such as polishing, coating, or texturing may also be employed to enhance the bar's performance or appearance. For instance, some applications may require a smooth, mirror-like finish, while others might benefit from a textured surface for improved adhesion or thermal properties.
Quality Assurance and Testing
Quality control is a crucial aspect of tungsten bar production, given their critical applications in industries like aerospace and electronics. Manufacturers employ a range of testing and inspection methods to ensure the bars meet stringent quality standards. These may include: - Non-destructive testing (NDT) techniques such as ultrasonic inspection and X-ray radiography to detect internal defects - Mechanical testing to verify properties like tensile strength, hardness, and ductility - Chemical analysis to confirm composition and purity levels - Dimensional inspection using high-precision measurement tools - Microstructural analysis through metallography and electron microscopy Each tungsten bar undergoes rigorous quality checks to ensure it meets the specified requirements before being approved for use in demanding applications.
Conclusion
The production of tungsten bars is a complex process that combines advanced materials science with precision manufacturing techniques. From ore extraction to final quality control, each step plays a crucial role in creating high-performance tungsten bars that meet the exacting standards of industries ranging from aerospace to electronics. As technology advances, so too do the methods for producing these vital components, ensuring that tungsten bars continue to play a critical role in pushing the boundaries of what's possible in engineering and manufacturing. If you want to get more information about this product, you can contact us at rmd1994@yeah.net.